The app
easytrack app can be installed on both smartphones and tablets under Android or iOS
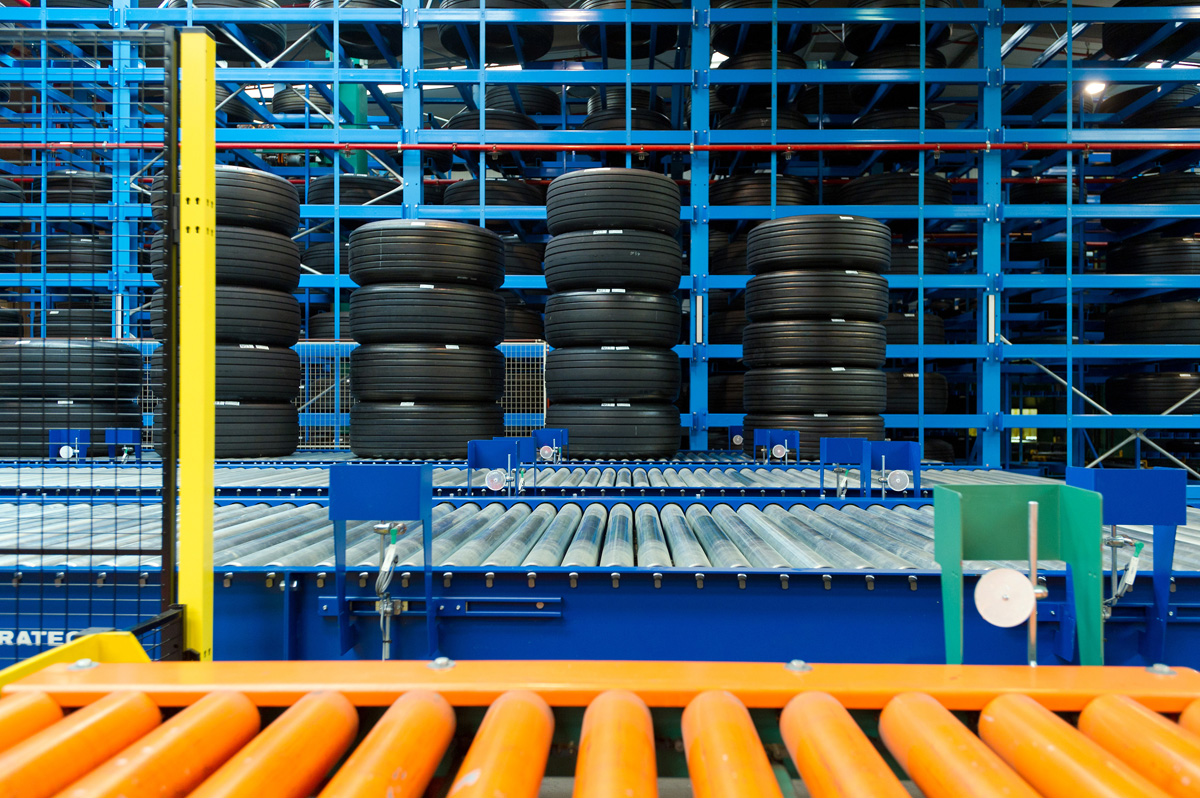
As tires arrive at the unloading bay, each unit is scanned using easytrack app and the serial number, invoice and certificate are seamlessly transferred to the customer system. No visual serial number identification or manual serial number input is required, only label scanning. All serial numbers shipped to a customer's warehouse are uploaded in to the Fixed Asset Management System or Desktop Module. No manual input required, no risk of incorrect serial number and a paperless e-document system save time and effort.
Tire certificates are available at any time from through the application. A simple label scan or click on the tire reference in easytrack allows easy document sharing through all usual communication channels.
Customers can file a damage report at any stage throughout the time the tire spends at the customers' facilities. The smartphone or tablet-based app will activate the camera and produce an editable image and text area that is then sent directly to Bridgestone. The Bridgestone Technical and Warranty teams will receive customer claims ins-tantly, offering improved response times and not requiring cumbersome email exchanges.
Reasons for removal can be selected from a pre-established list. Tires removed may be photographed, allowing a visual confirmation of the reason for removal (FOD, axle mat to a flat, etc.) to be stored in a secure easily accessible online database for future reference. The Landing Performance Tracking feature enables health trend monitoring and offers easy browsing through the reason for removal database.
Every outgoing batch can be built through the customer’s own repair administration module or can be drawn automatically from the most common MRO-focused FAMS. The batch is then sent to the warehouse worker’s smartphone as a task. Once all tires have been scanned (and loaded for shipping), the repair administrator and the Bridgestone team are advised the worntire batch (including individual unit details) is on its way and inbound for retreading. This way, a single set-format is used, allowing easy follow-up and shorter production times at Bridgestone.
Equipment and consumables are provided by Bridgestone. The exact moment when a worn tire label is generated can be customized to meet customer workflow requirements. The label can be generated by line maintenance or at wheel assembly breakdown in the shop for example. In all cases, only one single serial number visual identification is required and the operator’s/technician’s input is crossed checked in real time to eliminate the risk of serial number error. The label is then stuck on its tire and the tire once again becomes traceable through electronic scanning only. Only one database-checked manual operator input is required, reducing the risk of serial number input/reading error to the absolute minimum.
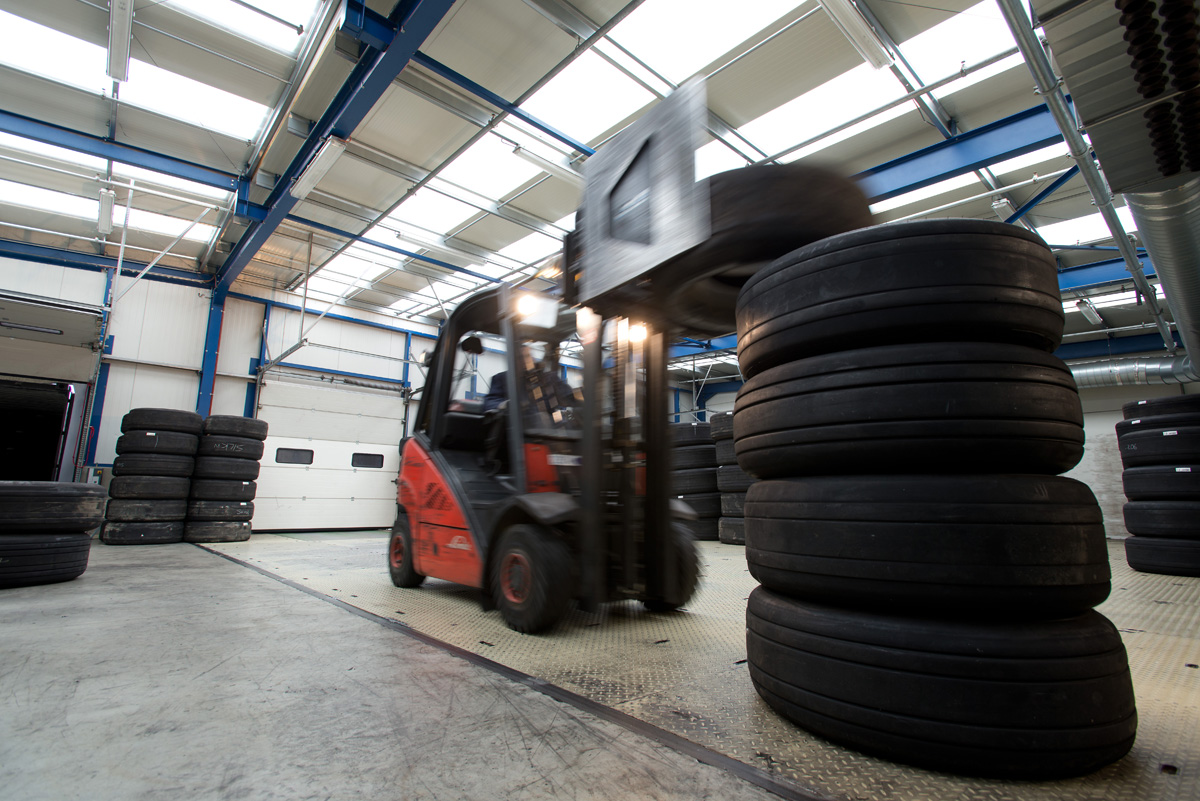